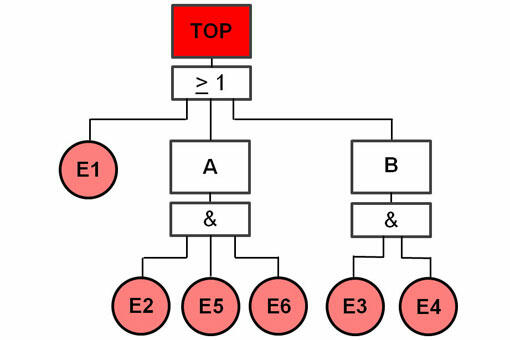
Fehlerbaumanalyse
Die Fehlerbaumanalyse ist eine deduktive Methode zur Analyse wichtiger unerwünschter Ereignisse (TOP-Ereignisse). In einem Top-Down-Verfahren wird ausgehend vom betrachteten TOP-Ereignis eine Baumstruktur entwickelt, in der das Zusammenwirken potentieller Ursachen für das unerwünschte Ereignis mit Hilfe von logischen Verknüpfungen dargestellt wird. Die Fehlerbaumanalyse kann den Entwicklungsprozess, die Festlegung einer geeigneten Systemarchitektur oder die Ableitung von Design-Anforderungen aktiv unterstützen. Die quantitative Auswertung erlaubt die Berechnung konkreter Zuverlässigkeitskenngrößen, wie z.B. die Wahrscheinlichkeit für das Auftreten eines Ausfalls.
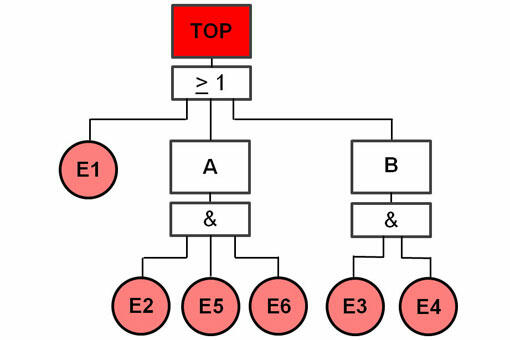
Fehlerbaumanalyse
Die Fehlerbaumanalyse ist eine deduktive Methode zur Analyse wichtiger unerwünschter Ereignisse (TOP-Ereignisse). In einem Top-Down-Verfahren wird ausgehend vom betrachteten TOP-Ereignis eine Baumstruktur entwickelt, in der das Zusammenwirken potentieller Ursachen für das unerwünschte Ereignis mit Hilfe von logischen Verknüpfungen dargestellt wird. Die Fehlerbaumanalyse kann den Entwicklungsprozess, die Festlegung einer geeigneten Systemarchitektur oder die Ableitung von Design-Anforderungen aktiv unterstützen. Die quantitative Auswertung erlaubt die Berechnung konkreter Zuverlässigkeitskenngrößen, wie z.B. die Wahrscheinlichkeit für das Auftreten eines Ausfalls.
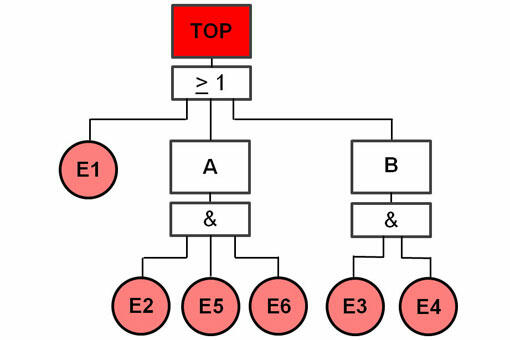
Einsatzmöglichkeiten
- Untersuchungsobjekte können Produkte, Systeme, Prozesse, Dienstleistungen oder Software sein.
- Analyse zentraler Risiken, die bedeutende Auswirkungen (Gefahren für Gesundheit und Leben, wirtschaftlicher Schaden usw.) mit sich bringen können. Beispiele dafür sind: Produktentwicklung in der Automobilindustrie, Planung von Industrieanalagen, vorbeugender Brandschutz, Sicherheitsprüfung kerntechnischer Anlagen
- Präventives Identifizieren möglicher Ausfallursachen in der Entwicklungsphase mit dem Ziel, das Auftreten dieser Ausfälle im Endprodukt zu vermeiden
- Analyse der Ursachenketten für aufgetretene Fehler (z.B. Ausfall einer Produktionsanlage), um so den Fehler in Zukunft zu vermeiden
- Sind die Ausfallwahrscheinlichkeiten von Komponenten oder Sub-Systemen bekannt, können Systemzuverlässigkeit und das Ausfallverhalten des Gesamtsystems quantitativ analysiert werden.
Ergebnisse
- Dokumentation systematischer Fehlerzusammenhänge in der Visualisierung als Fehlerbaum bzw. Fehlerbäume
- Liste aller möglichen Fehlerkombinationen, die zu einem unerwünschten Ereignis führen (sog. "Cut Sets")
- Liste aller minimalen Ausfallkombinationen, die zum TOP-Ereignis führen ("Minimal Cut Sets")
- Identifizierte Systemschwachstellen zur gezielten Optimierung
- Bei quantitativer Auswertung: Gesamtwahrscheinlichkeit für das Eintreten des unerwünschten Ereignisses und Zuverlässigkeitskenngrößen hinsichtlich Verfügbarkeit und Sicherheit
Vorteile
Sofort weiterlesen und testen
Erster Monat kostenlos,
dann 24,95 € pro Monat
-
Know-how von über 1.000 Profis
-
Methoden für alle Aufgaben
-
Websessions mit Top-Expert:innen
Durchführung: Schritt für Schritt
Produkte, Systeme, Software, Prozesse oder auch Dienstleistungen können mit Hilfe der Fehlerbaumanalyse untersucht werden. Der Ablauf ist bei allen Anwendungsfällen identisch. Zur besseren Lesbarkeit beschreiben die folgenden Schritte die Fehlerbaumanalyse eines technischen Systems, stellvertretend für alle anderen Untersuchungsobjekte. Die Analyse der Ausfallwahrscheinlichkeit wird hier nicht beschrieben.
Aus Gründen der einfacheren Lesbarkeit wird im Folgenden nur die grammatikalisch männliche Form (Teilnehmer, Moderator) verwendet. Es sind dabei aber stets Personen jeden Geschlechts gemeint.
Teamzusammensetzung
Besetzen Sie das Team mit erfahrenen Fachleuten aus den Bereichen, die mit dem System in Berührung kommen. Neben Entwicklung, Qualität oder Produktion können das der Kundendienst oder sogar Vertreter des Kunden sein. Berücksichtigen Sie bei der Auswahl, dass Ausfälle nicht nur durch Komponentenversagen, sondern auch durch Bedienfehler verursacht werden können.
Für die Moderation der Teamarbeit können Sie die Methode "Moderation von Arbeitsgruppen" einsetzen.
Schritt 1: Analysieren Sie Ihr System!
Definieren Sie den Umfang des zu untersuchenden Systems und beschreiben Sie es. Am besten geeignet ist dafür die Form eines Blockdiagramms. Sie können mit einer Black-Box beginnen und diese dann schrittweise von oben nach unten in feinere Teilsysteme zerlegen (Bild 1).
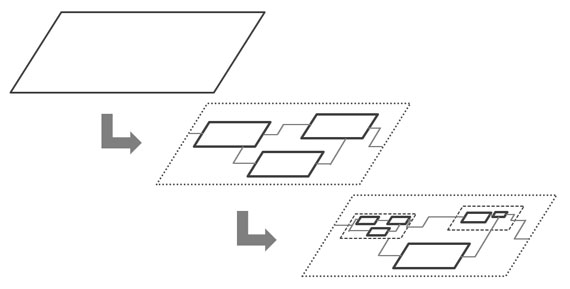
Bild 1: Schrittweise Verfeinerung des Systems top-down in immer kleinere Teilsysteme
Die Teilsysteme stehen über Eingangs- und Ausgangsströme miteinander in Beziehung. Diese Schnittstellen müssen mit ihren Toleranzen identifiziert werden. Dies können Signale (elektrisch, optisch…), Materialflüsse (Gas, Flüssigkeit…) oder Energie (Heizung, Kühlung…) sein. Ermitteln Sie die Umgebungsbedingungen sowohl des Gesamtsystems als auch der einzelnen Sub-Systeme (Temperatur, Druck, Feuchtigkeit…).
Sie erhalten so ein Systemblockdiagramm bzw. Funktionsblockdiagramm, bei denen die einzelnen Sub-Systeme und Komponenten miteinander in Beziehung stehen und die Organisation und das Verhalten des Gesamtsystems verdeutlichen. Um die Fehlerbaumanalyse effizient und wirtschaftlich zu gestalten gilt es bei der Erstellung des Blockdiagramms unbedingt auf zwei Aspekte zu achten:
1. Selektion der wesentlichen Elemente – Systemgrenzen
Identifizieren Sie die wesentlichen Elemente des Systems. Dies sind kritische Teilsysteme, die hohe Anforderungen zu erfüllen haben, bekanntermaßen risikobehaftet sind oder neue Technologien beinhalten, über die keine Erfahrungswerte vorliegen. Die Auswahl der relevanten Sub-Systeme kann z.B. durch eine Nutzwertanalyse oder Portfolio-Analyse erleichtert werden. Fokussieren Sie die Fehlerbaumanalyse auf diese Elemente.
2. Granularität des Blockdiagramms – Systemtiefe
Wählen Sie eine passende Auflösung der Sub-Systeme und Komponenten. Eine zu grobe Aufschlüsselung geht auf Kosten der Gründlichkeit, eine zu feine Aufschlüsselung erhöht den Aufwand enorm und liefert nicht unbedingt bessere Ergebnisse. Die Wahl der Granularität ist abhängig vom Ziel der Fehlerbaumanalyse: Um eine erste Systemabschätzung zu erhalten, genügt eine grobe Aufschlüsselung. Für die Analyse eines konkreten Designs ist eine feinere Auflösung bis in einzelne Komponenten sinnvoll.
berner
23.04.2018